We specialize in strengthening
America’s roadways
With decades of unparalleled expertise, Specialized is the industry’s leading full-service Pavement Maintenance & Construction company dedicated to providing communities with incomparable quality, performance and customer satisfaction.
PROCESS TREATMENTS
CRACK SEALING
Fiberized Crack Sealing is an important and cost effective pavement maintenance operation.
The polypropylene fiber, mixed with asphalt cement, adds strength to provide a long lasting seal from harmful moisture.
This method is an ODOT specification 423, Type III and has been a mainstay in Specon’s arsenal of pavement maintenance tools.
Applications can range from highways to municipal streets as well as parking areas.
Traffic is easily controlled and the risk of tracking is minimized as the material is wet-rolled.
-
Ductile in cold temperatures
High tensile strength for heavy loads
Prevents water intrusion into sub base
Most economical pavement preservation process
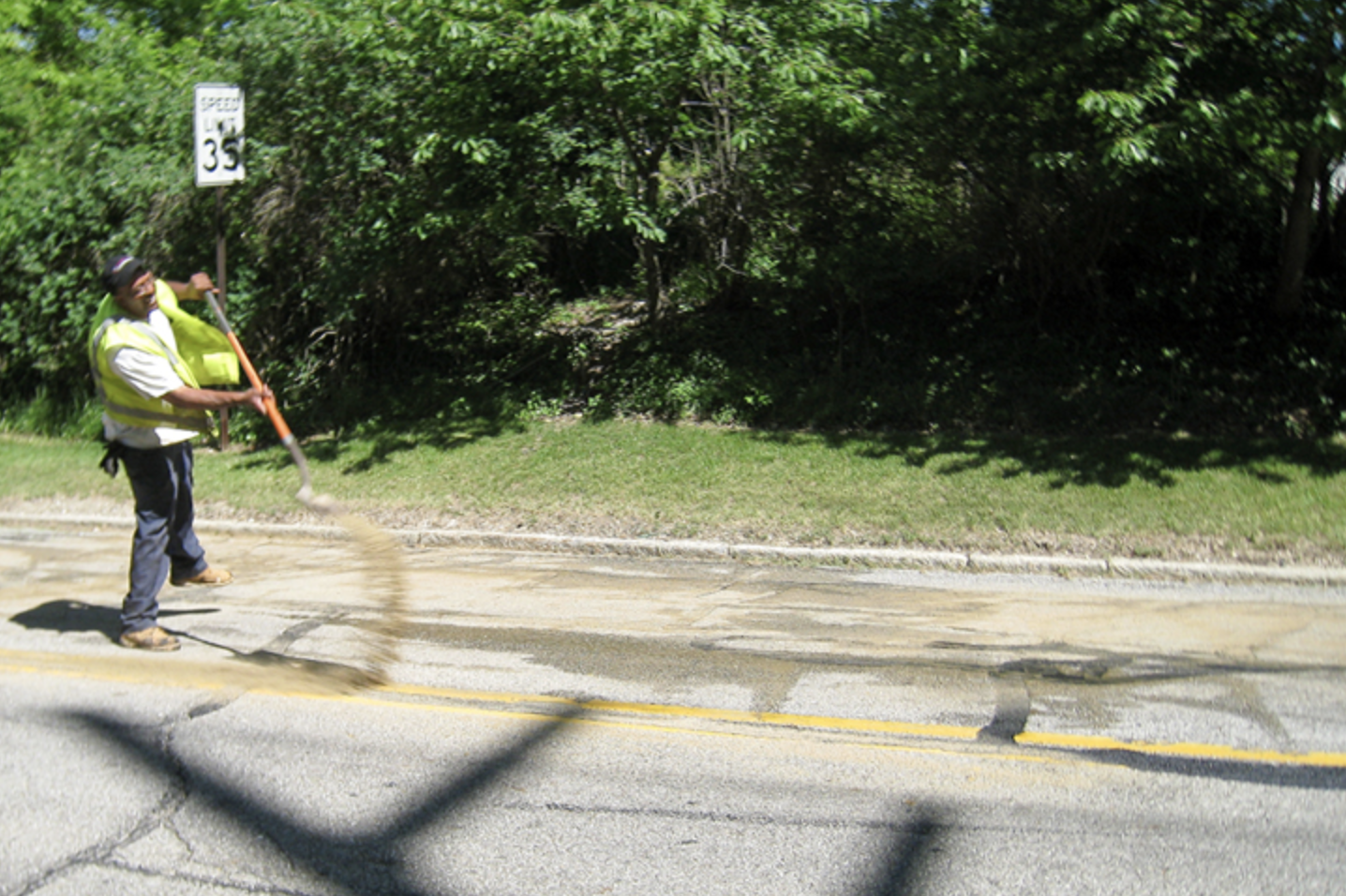
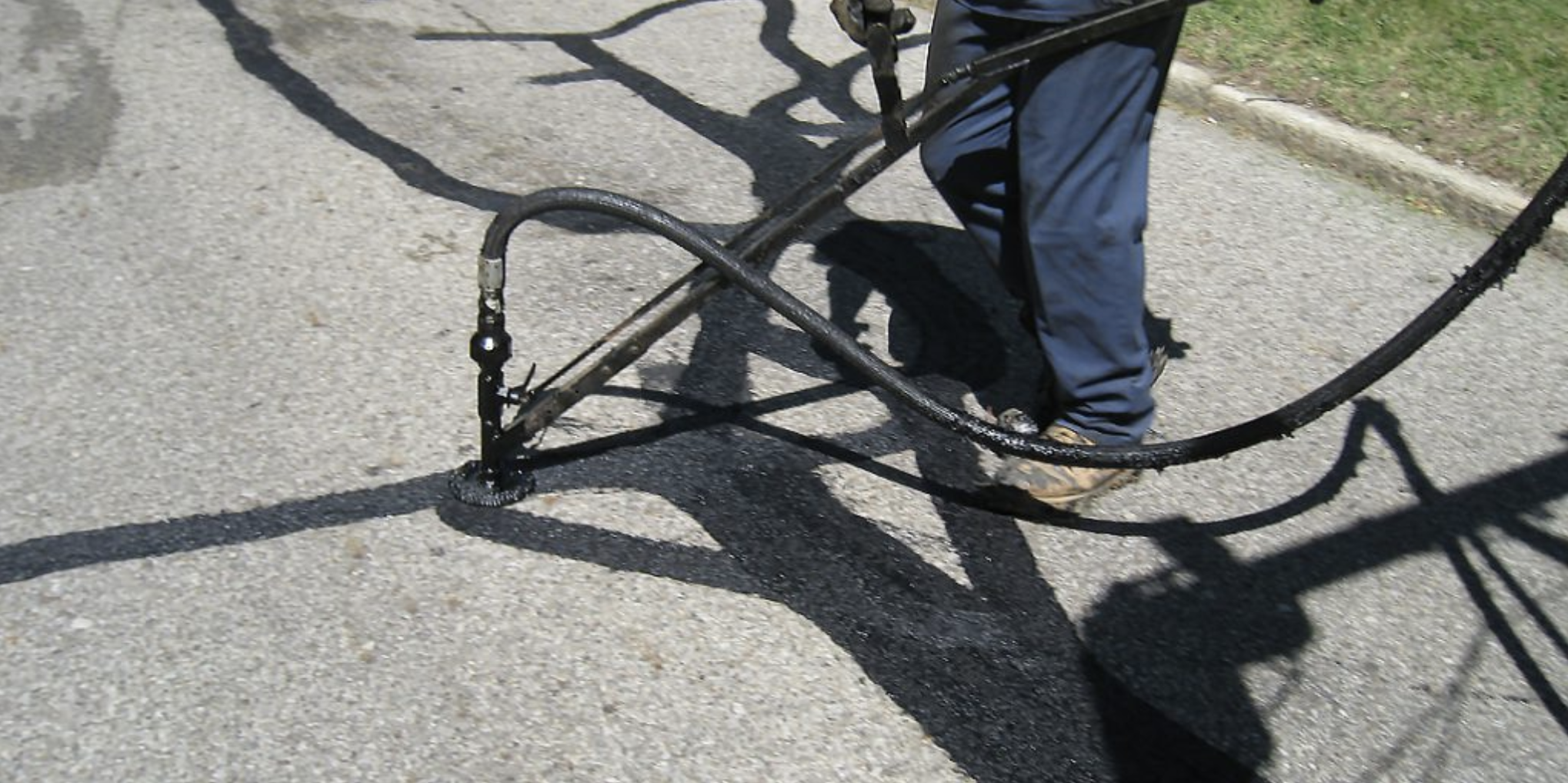
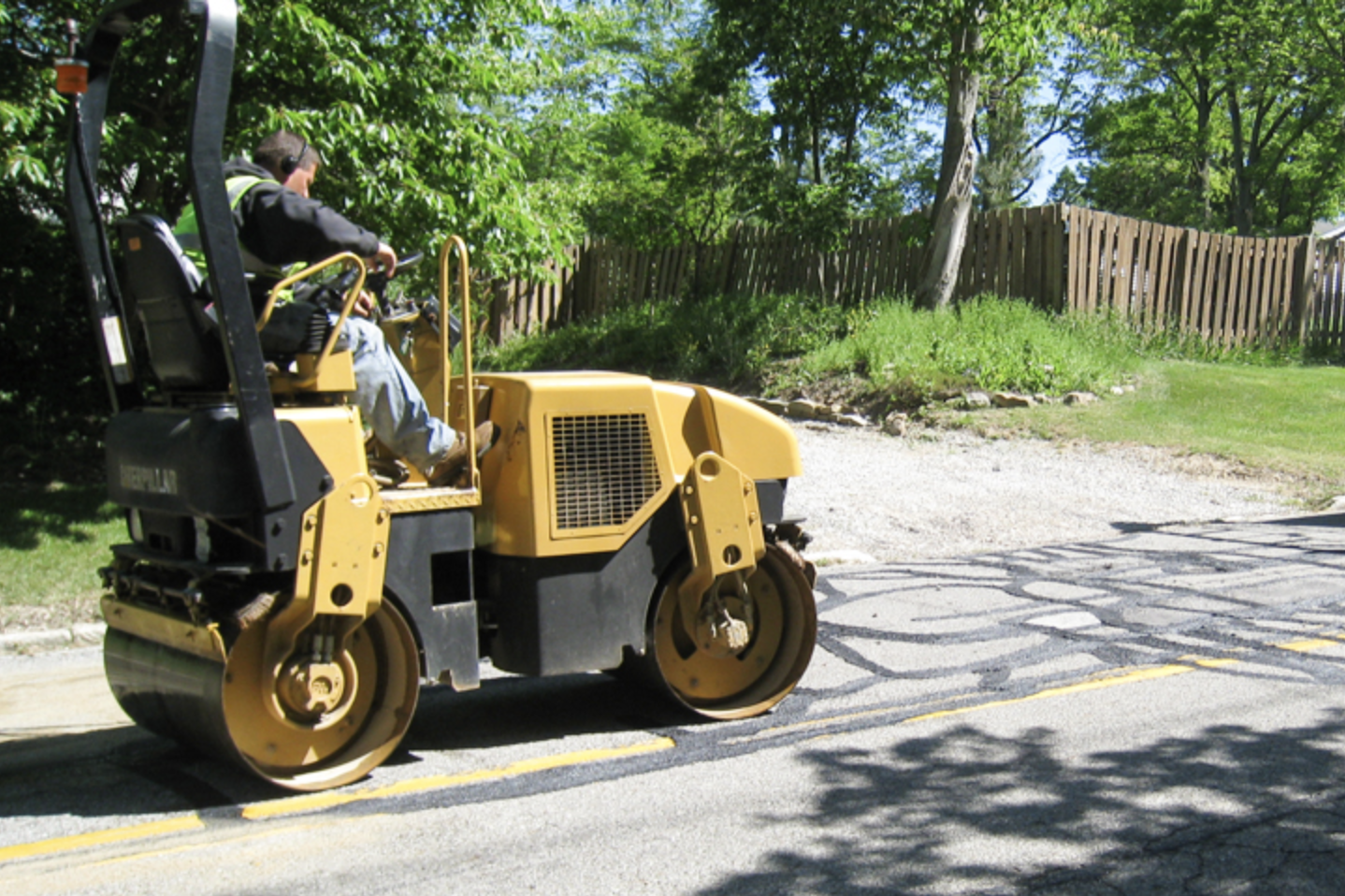

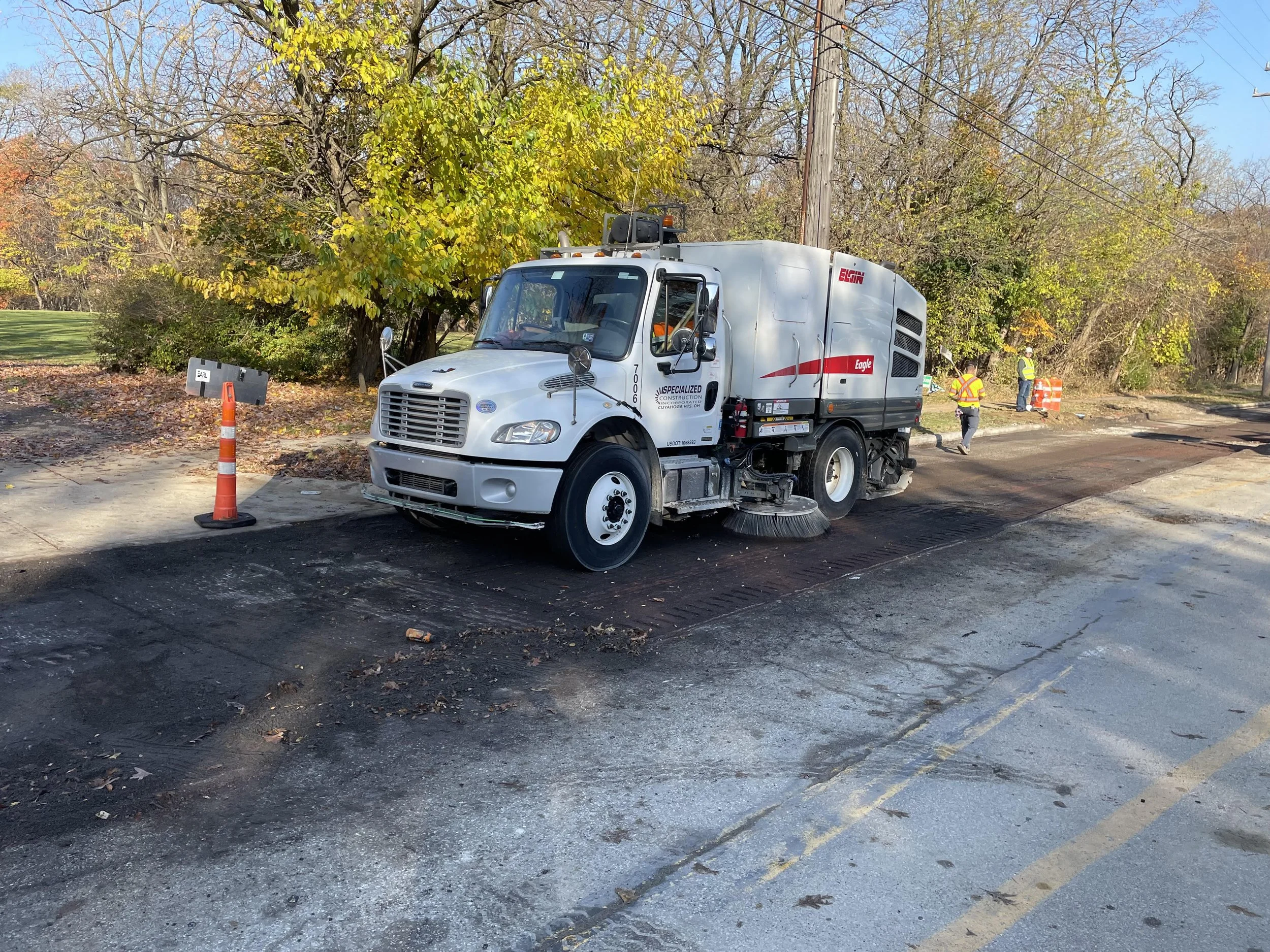
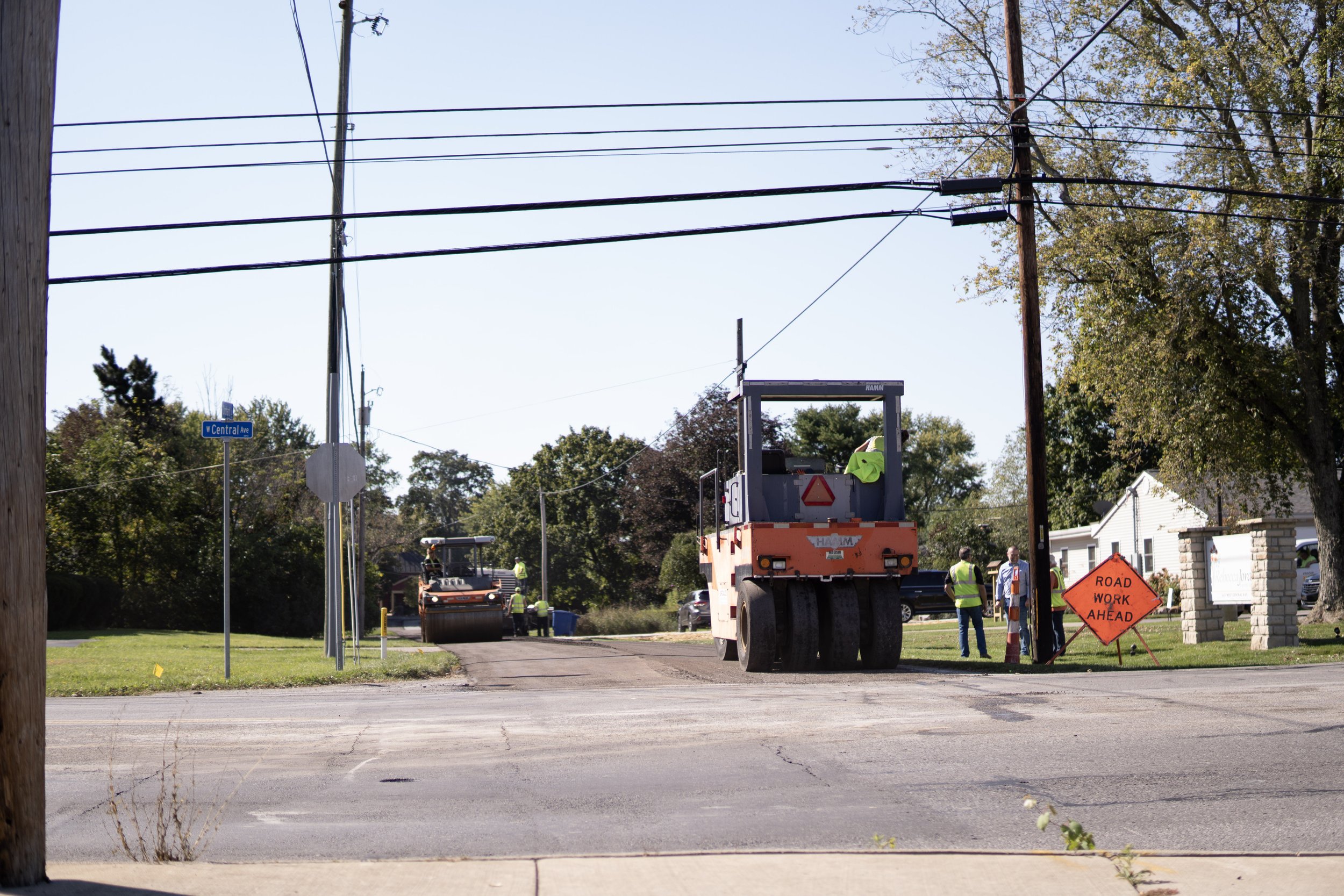
COLD IN-PLACE ASPHALT RECYCLING
Cold In-Place Asphalt Recycling is a rehabilitation technique in which existing materials are injected with a recycling agent and used in place. The materials are mixed in place without the application of heat.
The single pass equipment is capable of breaking, pulverising, and adding recycling agents in a single pass. Virgin aggregate, if required, can be spread on pavement surface, and included in the recycling operation.
Advantages include superior gradation of the recycled material, less disruption of traffic flow, in that the roadway is never closed, and full depth elimination of the pavement cracking pattern.
The primary benefits of cold inplace recycling include significant structural improvement by improving the existing pavement materials, treatment of most types of pavement distress, and improvement of ride quality.
We are equipped with the Writgen 2100/2200 Series Cold Recycling Machine, so the pavement is recycled to a specific gradation, liquid emulsion additive introduced to the grindings, and the material augured through a vibrating screed.
-
Conserves energy and natural resources
Environmentally friendly
Improves mix characteristics
Cracking eliminated
Improves cross slope
Cost effective
Saves time
May be performed under traffic
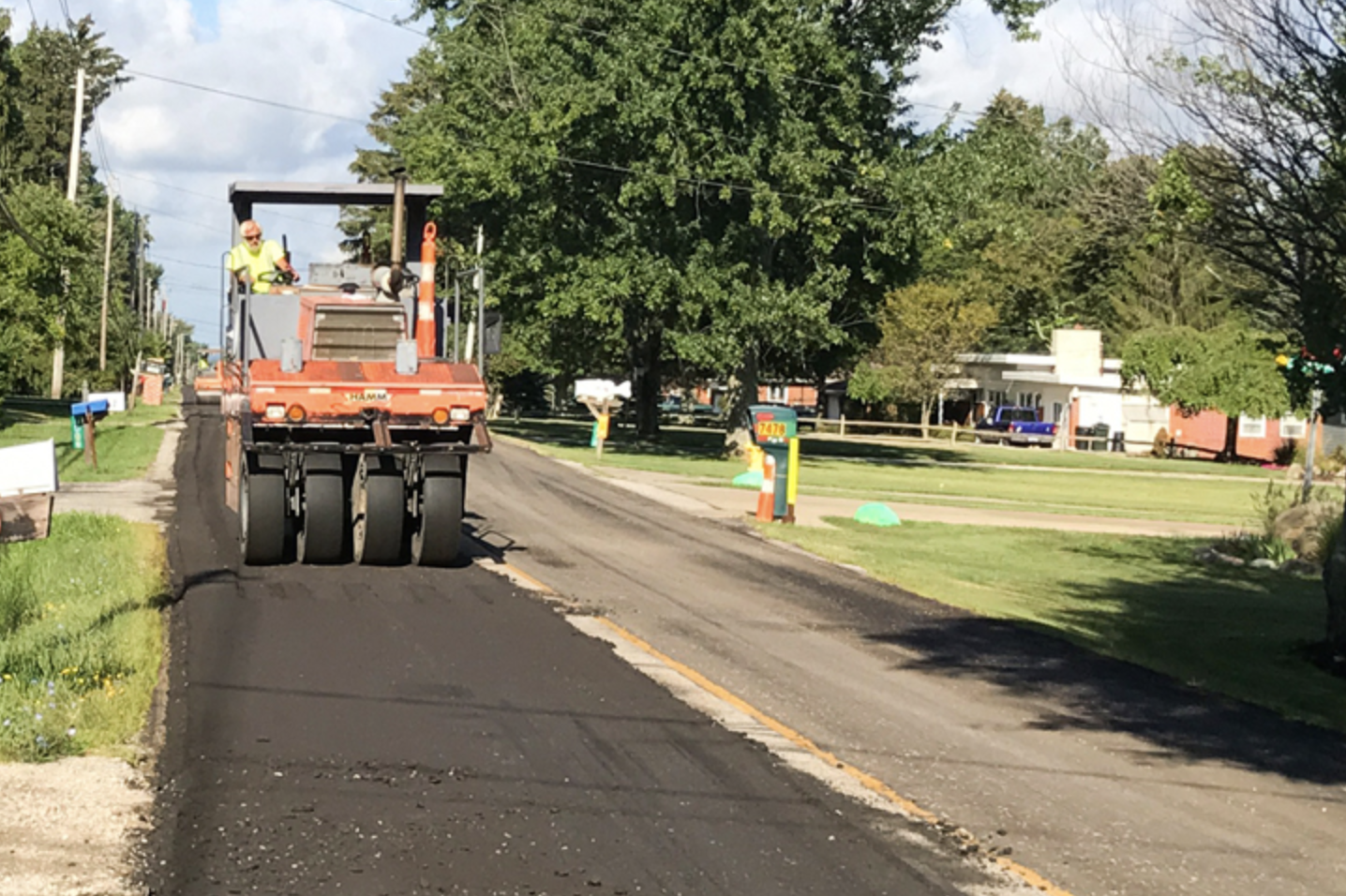
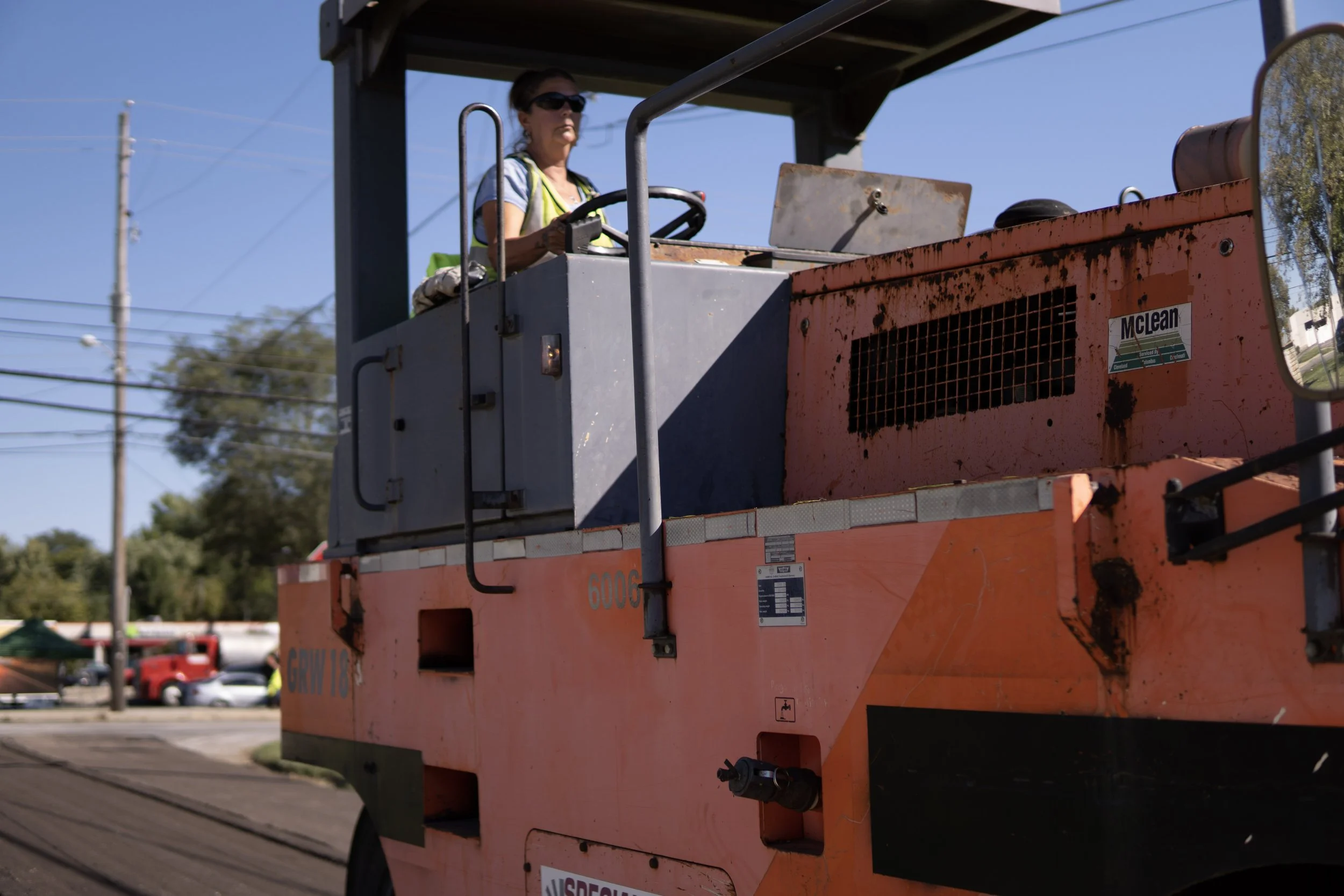
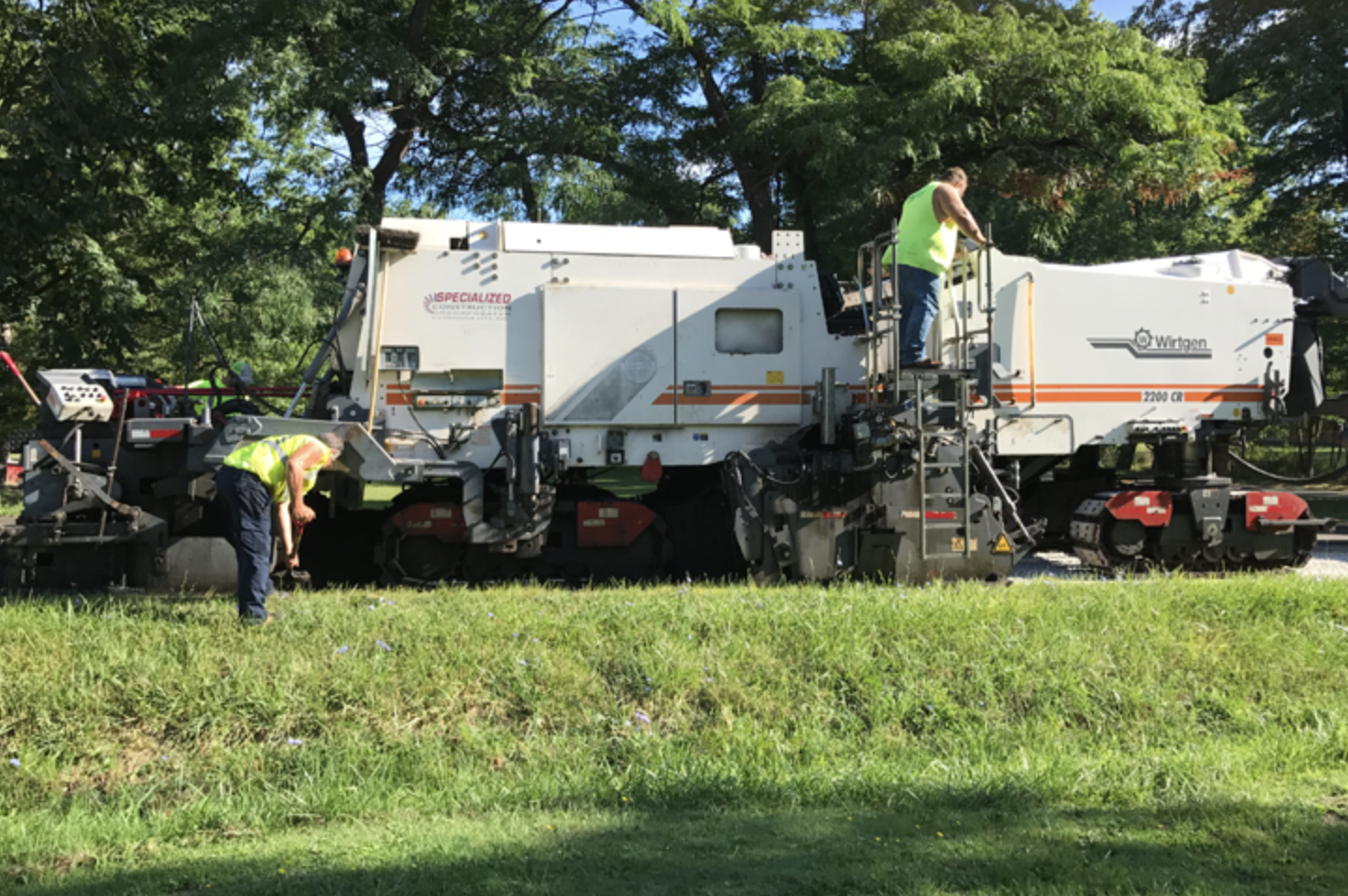
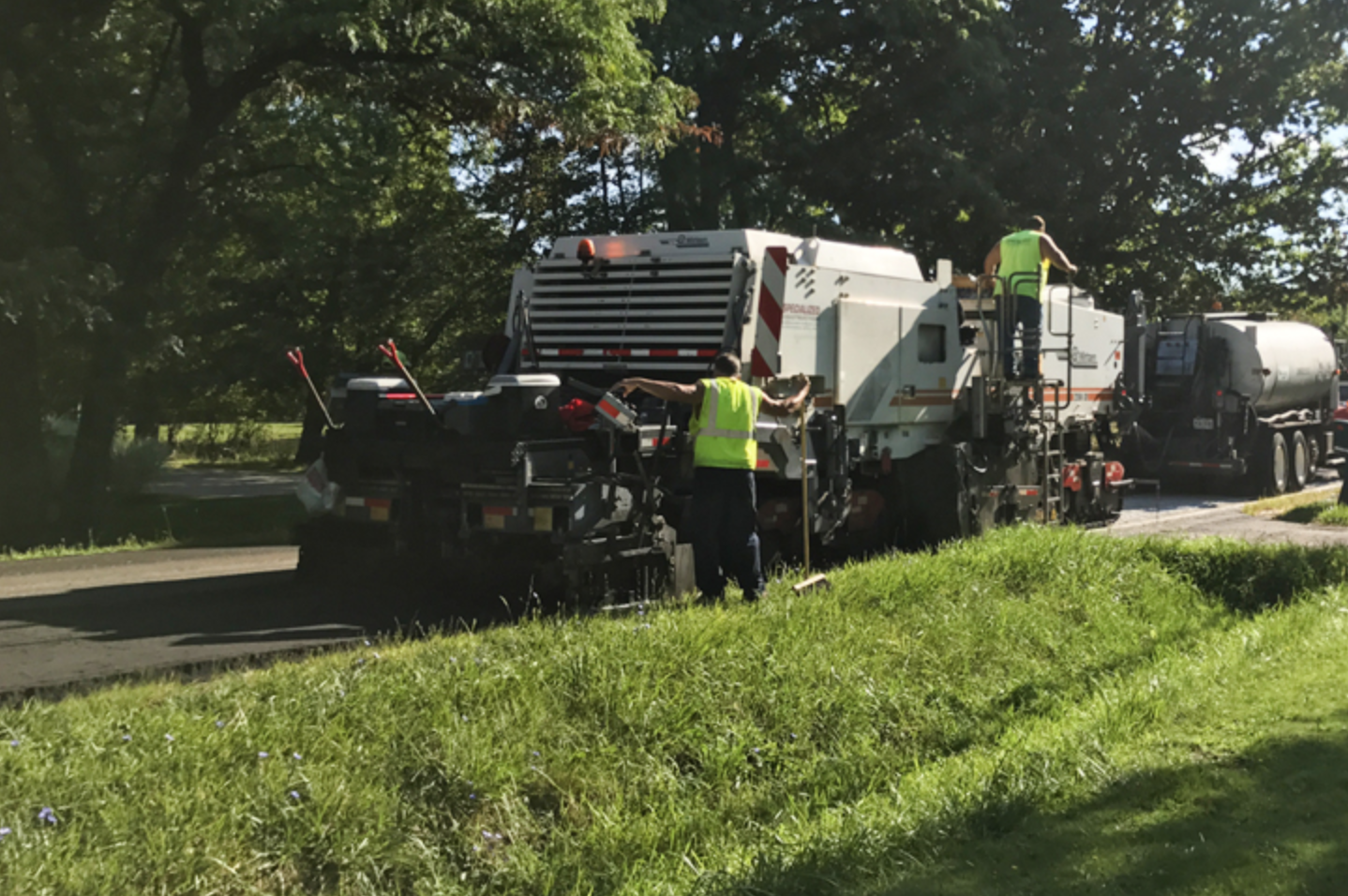

Watch us work
Here is what a segment of Cold In-Place Single Pass Asphalt Recycling process looks like.
CHIP SEALING
Chip Sealing is a cost effective method of maintaining roadways for communities. As an alternative to asphalt overlays, it is usually ¼ of the cost, and generally allows traffic to use the roadway sooner.
Chip Sealing is a pavement preservation process in which a binder is applied to an existing asphalt road and followed by an application of embedded aggregate. This in turn, provides a safe, skid-resistant surface while minimizing reflective cracking.
Chip Sealing with flexible binding emulsion (FBE) CRS2-P with 4% polymer and #8 pre-coated air-cooled blast furnace slag, offers superior performance as a wearing course. This specification used in conjunction with a fog seal offers an “asphalt paved” look to any roadway.
-
Excellent skid resistance
Great durability
Prevention of minor raveling
Seals cracks and water penetration points
Extremely cost effective vs. traditional overlays (approximately one quarter of the cost)
Quick setting and minimal traffic disruption
Why use Chip Seals?
The difference is in the construction method.
Hot Mix Asphalt pavement is produced by heating liquid asphalt and mixing it with aggregate, with the mix then spread and compacted to form a durable road structure and riding surface. Chip Sealing uses the same ingredients as asphalt concrete paving, but the construction method is different. Liquid asphalt binder is sprayed on the road surface, followed by the placement of small aggregates (“chips”). The chips are then compacted to orient the chips for maximum adherence to the asphalt, and excess aggregates is swept from the surface. Hot mix asphalt and chip seals are the same; only the construction methods are different.
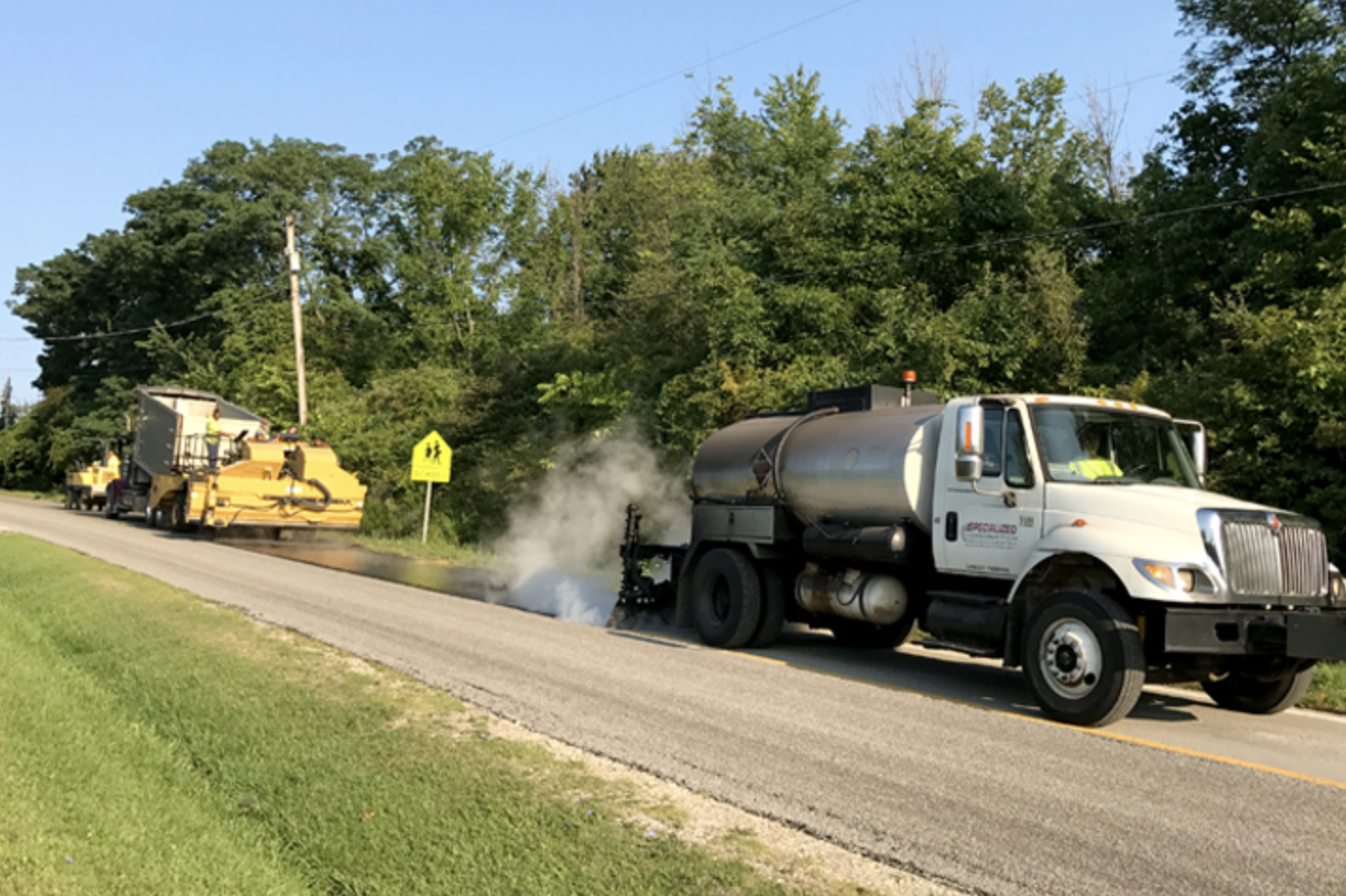
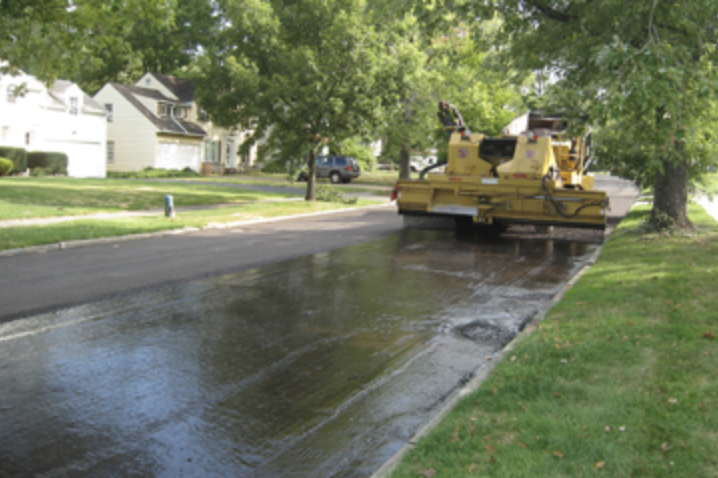
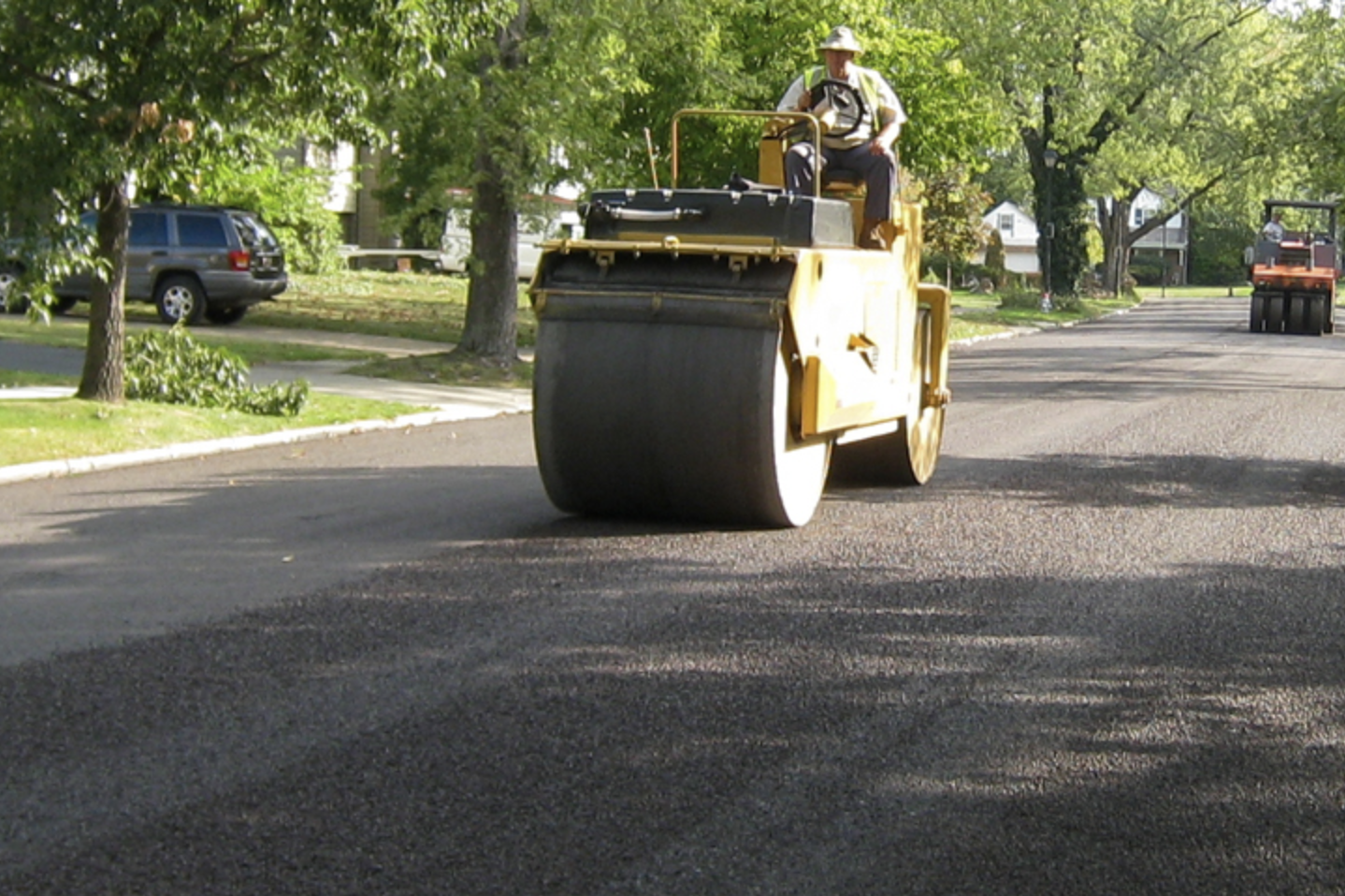
11 REASONS TO USE CHIPS SEAL
-
1
Chip seals provide agencies with the opportunity to maintain the roads for very low cost.
-
2
A chip seal is about one fourth to one fifth the cost of a conventional asphalt overlay.
-
3
By extending the time between asphalt overlays, chip seals result in lower costs over the long term.
-
4
By placing a chip seal sooner than an asphalt overlay would be placed, the traveling public benefits from roads maintained in better condition.
-
5
Chip seals eliminate the need to crack seal.
-
6
Chip seals enhance safety by providing good skid resistance.
-
7
Chip seals provide an effective moisture barrier for the underlying pavement against water intrusion by sealing cracks in the pavement.
-
8
Chip seals prevent deterioration of the asphalt surface from the effects of aging and oxidation due to water and sun.
-
9
We have successfully used chip seals for over 25 years to maintain state routes.
-
10
Chip seals virtually eliminate black ice.
-
11
In hot weather, chip seals re-seal cracks by flowing back together.
FOG SEALING
Fog Sealing consists of applying a newly chip sealed roadway with a special polymer emulsion.
The benefits include a superior retention of the chip seal aggregate and providing a water resistant surface.
This process is quick drying and less susceptible to tracking.
-
When Chip Sealing is followed by fog sealing, the life of the chip sealed road is expected to increase
Provides lasting protection
Reduces loose stones
Increased embedment of cover material
Accelerated curing of completed project
Decreased snowplow damage
Locks down marginally embedded chips
Reduced raveling
Prolongs the service life
Quicker snow and ice melt
Improved pavement marking visibility
Appearance preferred by traveling public
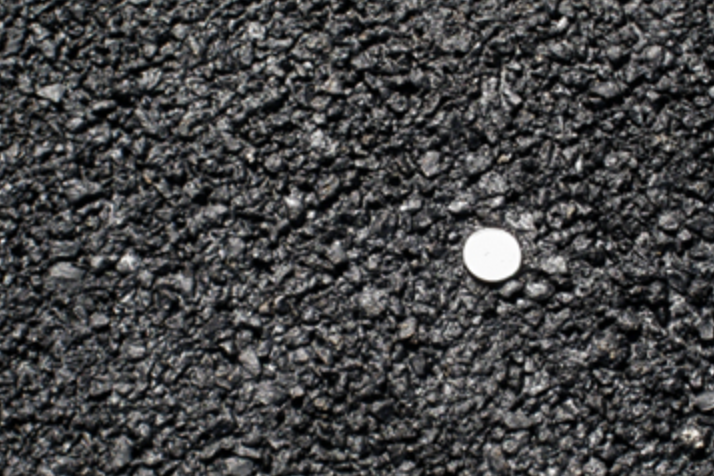


MASTIC SURFACE TREATMENT
Axys®/Onyx® or “Mastic Surface Treatment”, combines the durability you want from a pavement maintenance application with frictional characteristics achieved through aggregate inclusion.
Axys®/Onyx® can improve the micro-texture on a variety of Asphalt Surfaces, or “lock down” loose aggregate and eliminate dust associated with Chip Seal surfaces.
PRODUCT DESCRIPTION Axys®/Onyx®, installed at 0.20-0.25 gallons/square yard, is a mixture of polymer modified asphalt emulsion, quality “fine” aggregate, dark color enhancers and breaking and setting additives. Axys®/Onyx® is designed to protect your investment, minimize the costs of future maintenance treatments and get traffic back on the roadways more quickly.
-
ECOLOGICAL – No offensive coal tar seal smell
FRICTION – Aggregate inclusion within polymer modified emulsion
LONG SERVICE LIFE – Typical service life expectancy is 3-5 years
LONG LASTING DARK COLOR – Resists UV damage to remain dark for the life of the product
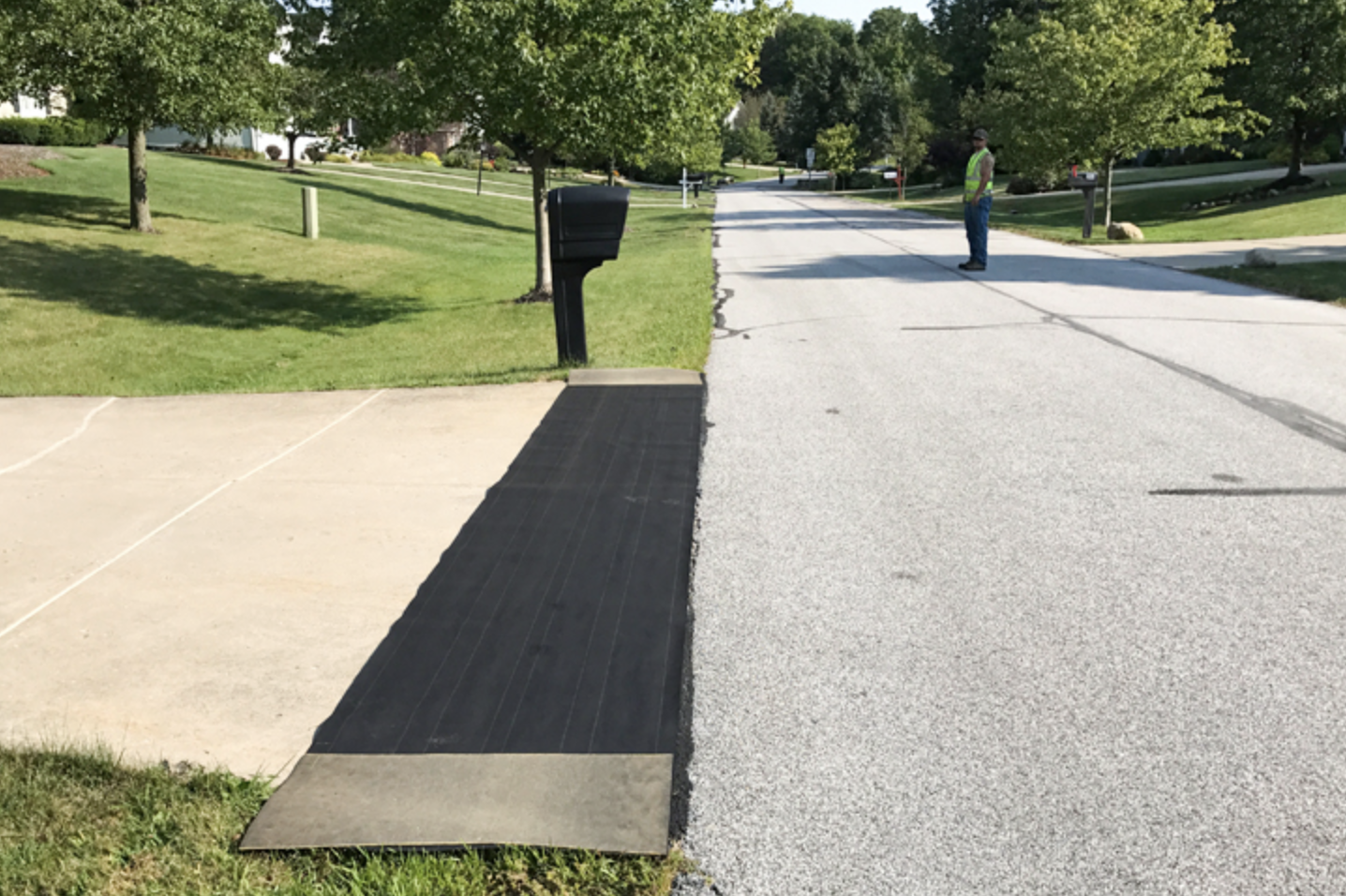
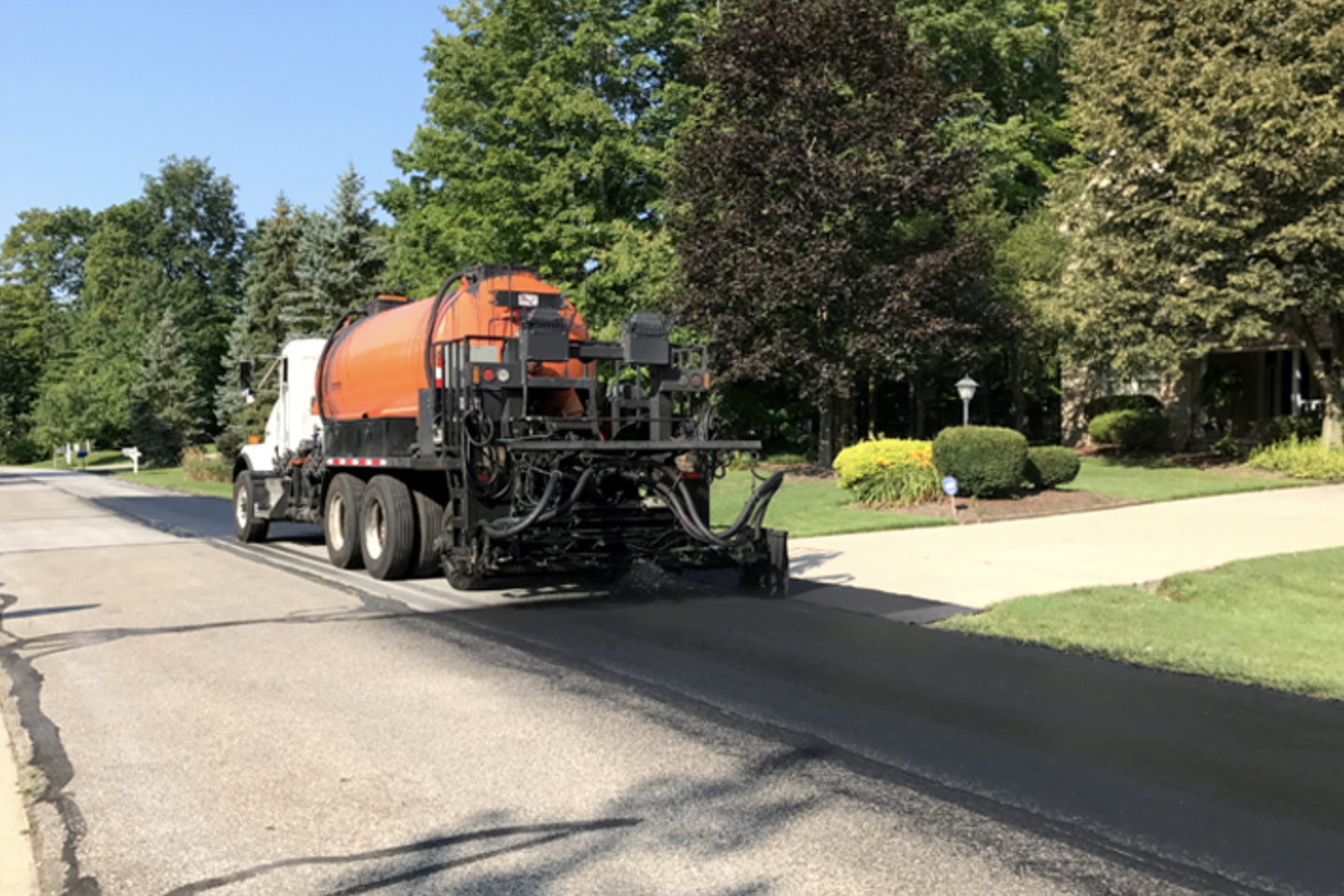
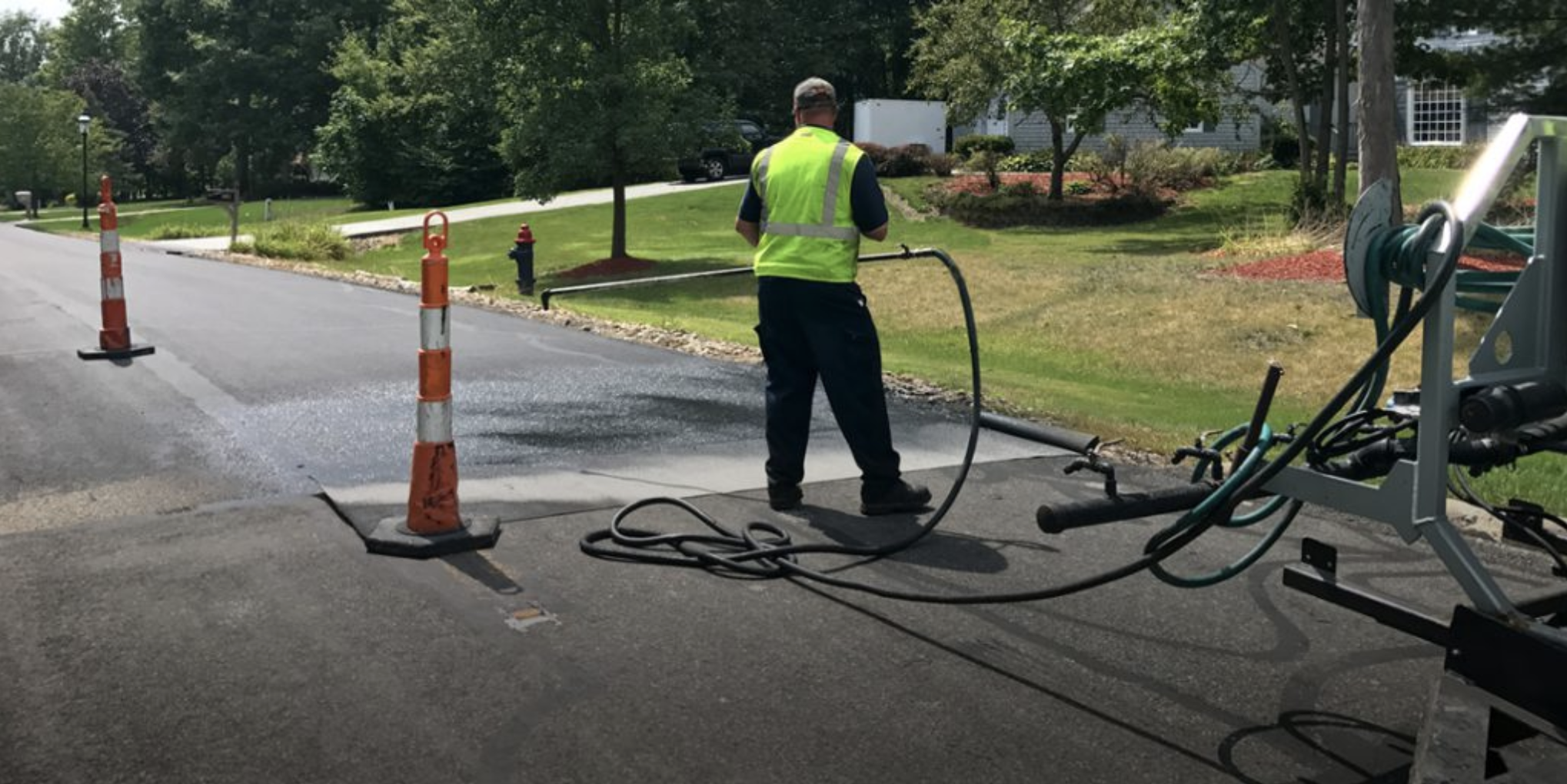
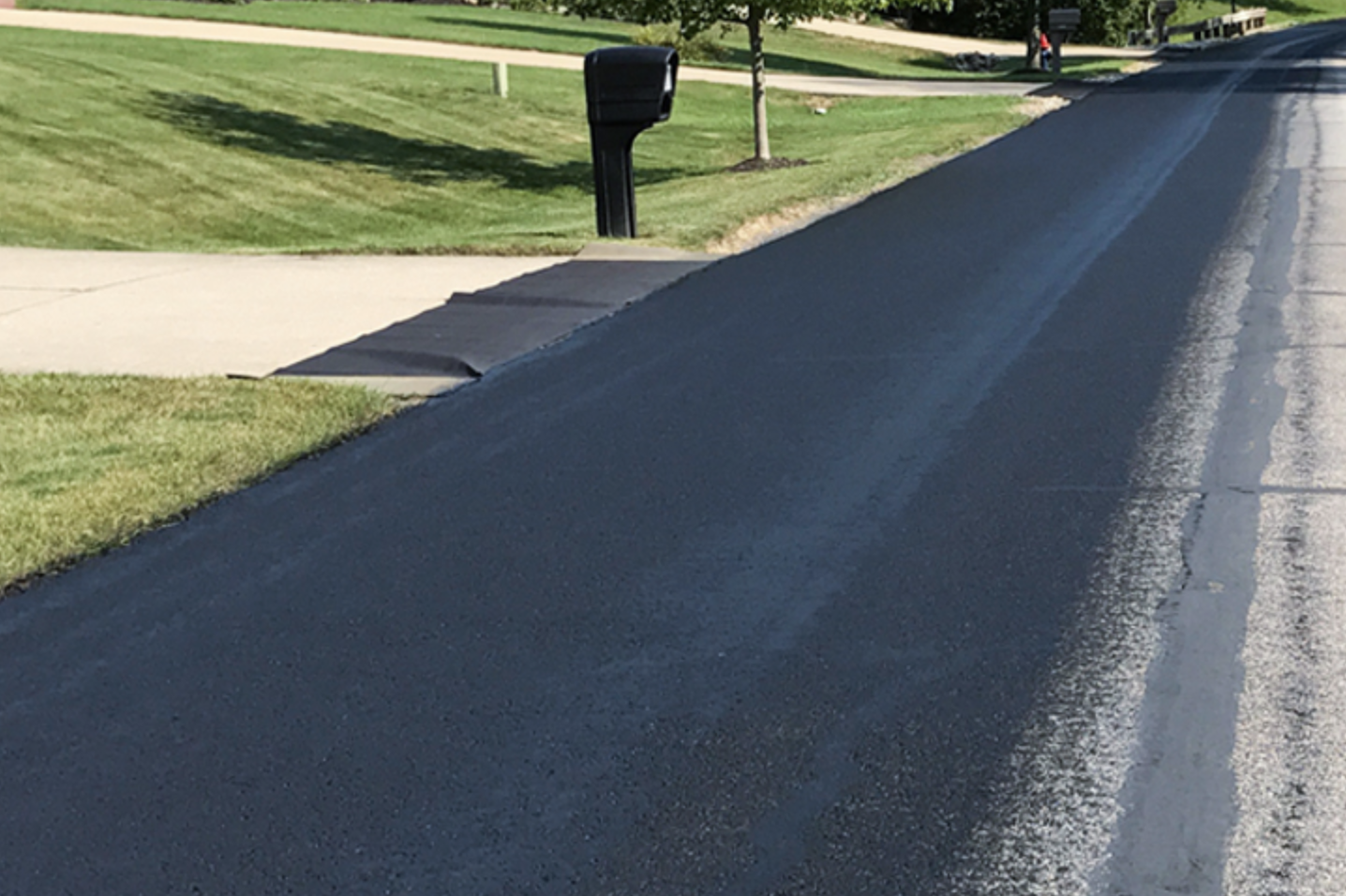
VOID REDUCING ASPHALT MEMBRANE
A Void Reducing Asphalt Membrane (VRAM) is placed in the form of a heavy membrane under the intended area for an overlay construction joint, either 12” or 18” wide and with thickness up to 5/32”.
The VRAM then migrates into the high air voids in the HMA overlay in the area of the longitudinal construction joint and reduces voids to more typical HMA range.
The VRAM is suitable for construction traffic to drive on without pick up or tracking within 30 minutes of placement.
Click below for more information about a recent project:
Successful VRAM Application on SR-62 in Licking County, OH
-
During construction:
• Upward migration
• Non-tracking
• Resist Flow
• Crack resistance
• Reduces water and air permeability
• Bonds to existing pavement
• Longitudinal joint issues
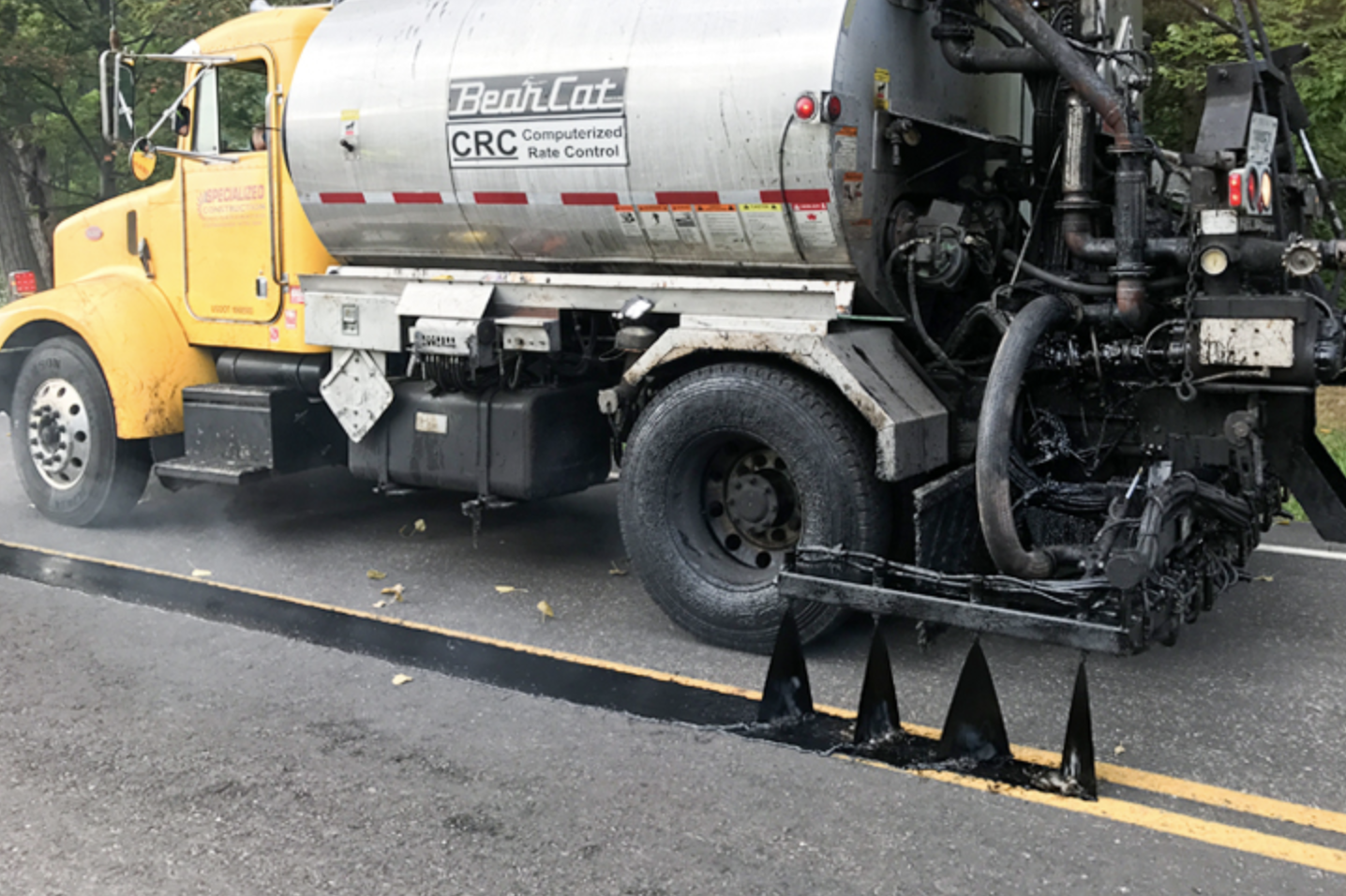
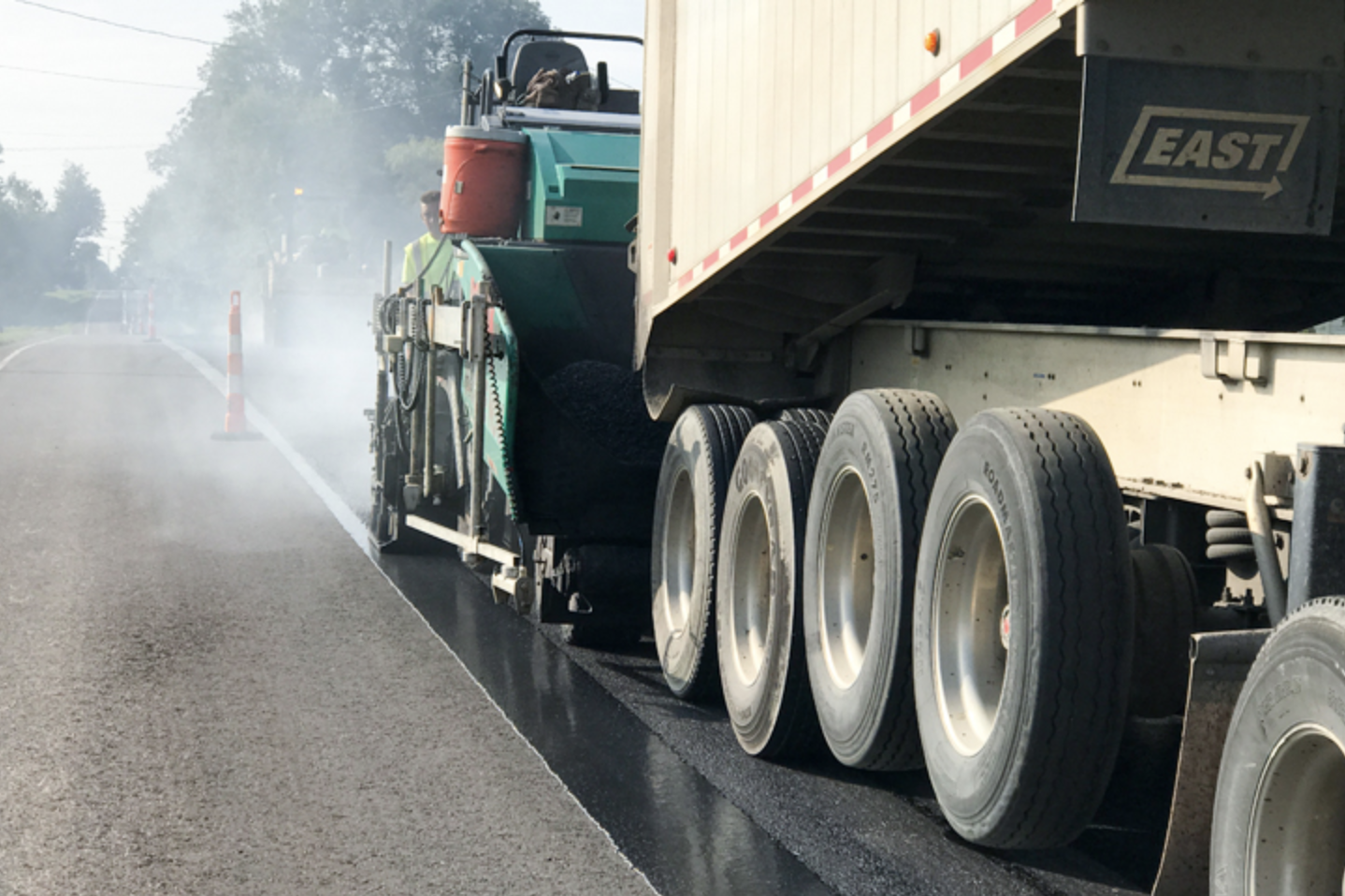
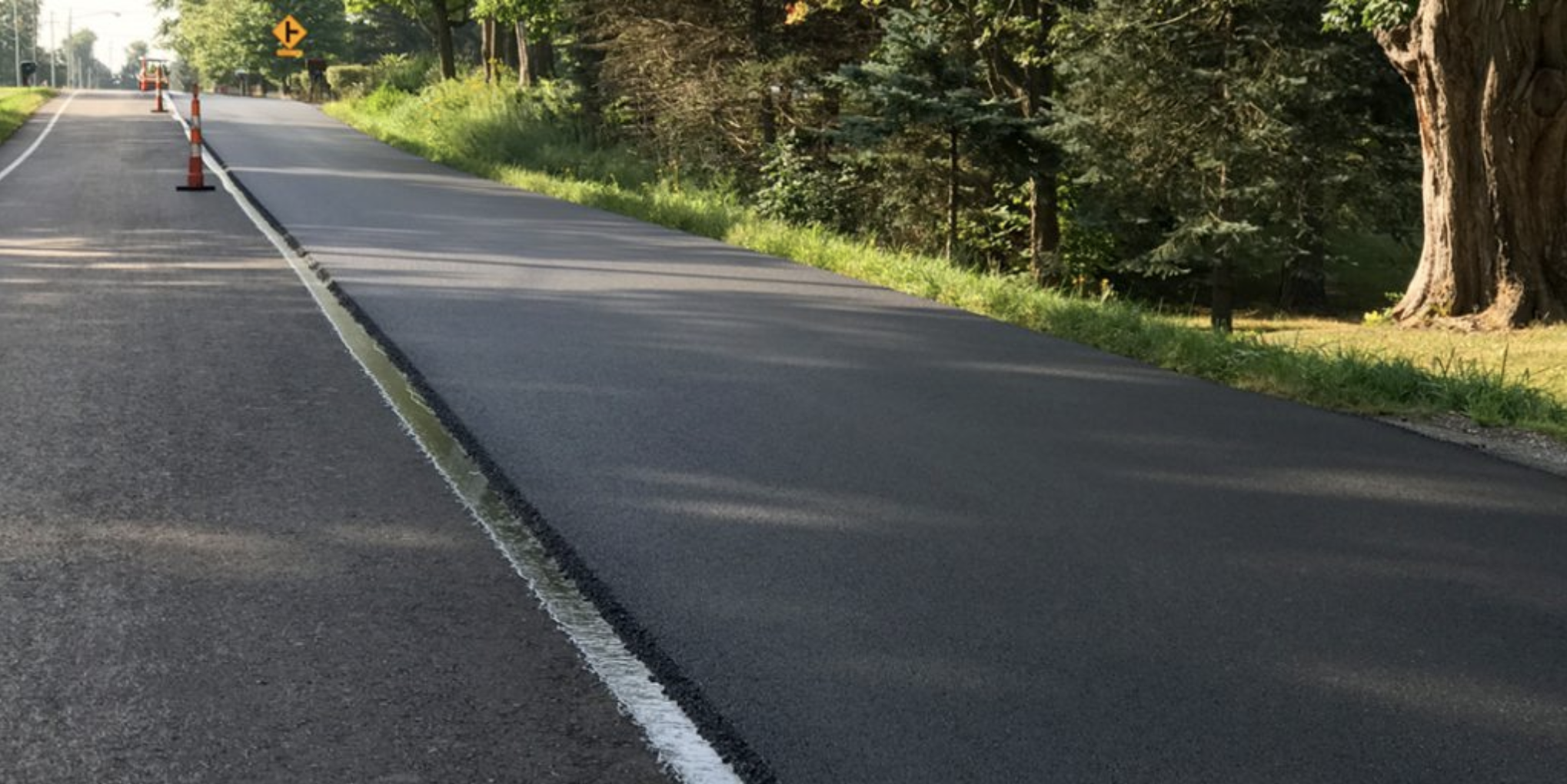
PAVEMENT PLANING
Asphalt Planing refers to the act of mechanically removing asphalt by way of a pavement planing machine.
This description refers to an industry standard modern cold planing model, though many different sizes and types of planers exist. An asphalt cold planing or milling machine consists of the following primary components: The milling drum, the milling drum housing, the engine, the conveyor belt, water tank, crawler tracks, and operator’s platform.
Also referred to as “Asphalt Milling”, Cold Planing (CP) is the controlled removal of the surface of the existing pavement to the desired depth, with specially designed equipment to restore the pavement surface to a specified grade and cross-slope.
CP can be used to remove part or all of the existing pavement layers.
We have a fleet of varying width machines available for this process. Included among them would be machines of 1’, 4’, 7’ and 8’ widths.
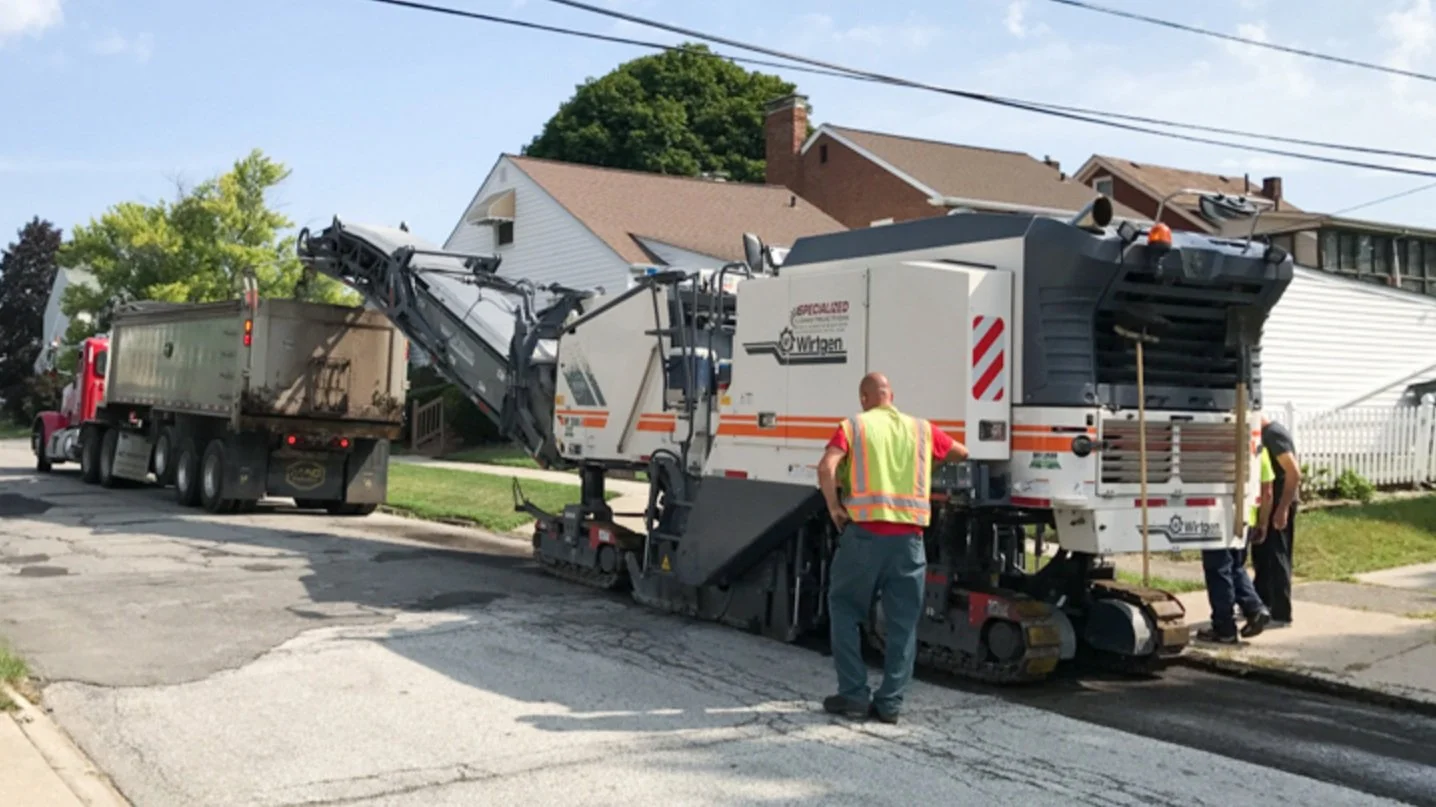
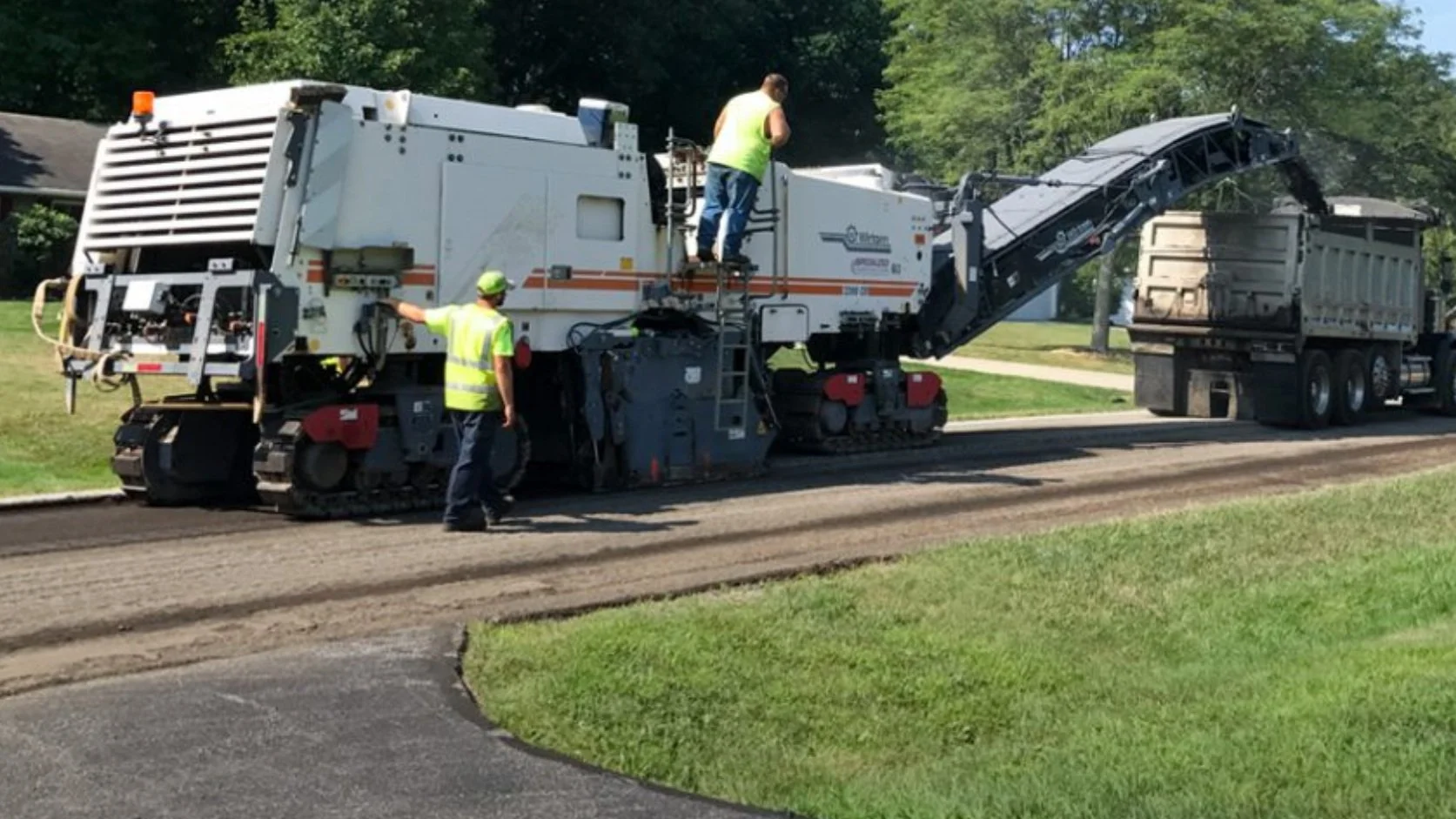

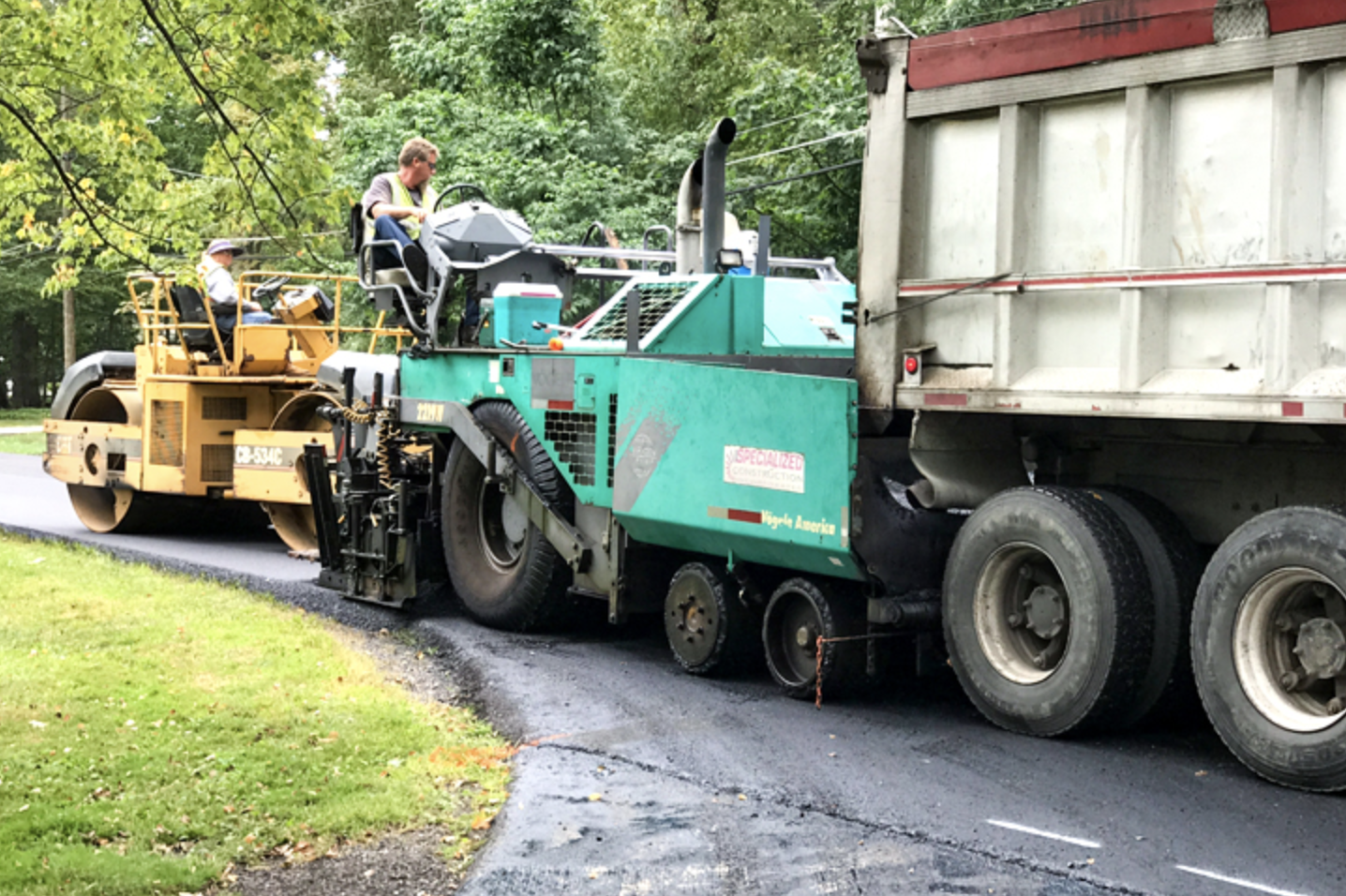

